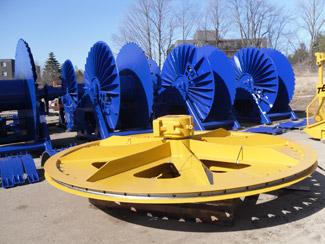
The mining equipment division of Timberland Equipment manufactures custom-engineered equipment capable of giving reliable service for 50 years. The company therefore relies on new markets and new mines for expansion.
Established in Woodstock, Ontario in 1947 to manufacture lifting equipment for the lumber industry, Timberland Equipment has since diversified into a number of complementary industries and has become recognized as an expert in each.
Its original roots are still evident in its continued production of tree trimmers, but the company’s core business today is the design and manufacture of specialized material handling equipment for the resource and energy sectors. With over 60 years of experience to draw on, Timberland has built a global enterprise based on high-quality rugged products with an outstanding reliability record and a long lifespan.
Woodstock is still the company’s headquarters, and from there it engineers and manufactures products for the mining, conductor handling and offshore divisions. The company also operates manufacturing sites in Sudbury, Ontario, Halifax, Nova Scotia and Shreveport, Louisiana in the United States, which specialize in products for other divisions.
Woodstock is conveniently located for the mining industry, with Ontario a major center for mining, mining services and equipment manufacturing. Gold production is centered on Ontario, while copper and nickel, often mined together, are found in most provinces.
The massive hoists, winches and sheaves that Timberland produces are generally custom-engineered for specific locations and uses, and they are designed to last. Some of the first pieces of equipment Timberland produced over 50 years ago are still in operation today and performing to exacting modern-day standards.
This industry is unlike many others, where products have a short lifespan and redundancy is built in to the design. Repeat customers do not come around every few years, so Timberland’s focus is not on the established mines—though there is a market for spare parts and refurbishing old equipment—but on new mines under development that are purchasing equipment for the first time.
In the dynamic Canadian mining sector, the Saskatchewan potash industry is a key target, and another is Quebec, where gold, copper and metals mines are actively being developed. Newfoundland also looks promising for the future.
The company is also very active in the US, with interests across many states including Idaho, Pennsylvania and Utah. North America currently accounts for the majority of Timberland’s mining business, but the greatest growth opportunities now lie in international markets. The company is already active in Peru, and has delivered mine rescue equipment to the rapidly growing market in China. Further expansion in China is high on the agenda, as is the lucrative South African market.
The global expansion drive is spearheaded through sales offices in Mexico and Beijing, and as part of the campaign the company has launched an extensive program of customer contact aimed at achieving 100 percent awareness of the Timberland quality and capability. An active schedule of travel, personal meetings and presentations is therefore under way and is focused at three levels. The company is communicating with the mine owners—the mining corporations and mining juniors who procure and pay for the equipment and expect value for money and equipment longevity; the engineering consultancy companies who focus more on the equipment specifications and operations; and the onsite contractors who are looking for reliability and dependability.
Mining equipment is an interesting field. Because the equipment is heavy and robust, the design of the basic mechanical parts has not changed much over the years, which is why they can last for so long. What does change more quickly is the technology involved in the controls and safety features.
Each country, state and province may have its own specific code requirements for controls and safety, and Timberland incorporates these into the design of new equipment, following up with a rigorous engineering review. All the mining products are engineered, manufactured and tested at the 50,000-square-foot facility in Woodstock, where pre-shipment commissioning is done before the product is broken down to component level to be packaged and shipped.
Having said that the basic components have not changed much, the way they are put together obviously does, because everything Timberland builds is custom-designed for a specific application, meaning that every product is a new solution. Every new design then becomes a proven product and part of an extensive design portfolio, which may then be used as the basis for further developments in the future.
Timberland is also responding to recent changes in the economics of the mining sector. With rising metals prices, mining of previously uneconomic resources is now becoming feasible, and mine owners are keen to increase the lifespan of new and existing mines by exploring and mining at deeper levels, extending the tunnels and drifts for a greater distance. Consequently, Timberland’s products are now required to do more, do it faster, go deeper underground and last longer. These are all challenges that give the company opportunities for growth.
Looking to the future, the company is planning to further improve and capitalize on its extensive business within North America and is continuously updating its engineering and manufacturing facilities to complement this. For the past five years the manufacturing operations across the group have been continuously improving their throughput through the implementation of the Theory of Constraints, and this has enabled the company to increase its record for on-time delivery and to meet increasing demand without the need to expand the plant and facilities.
Meanwhile, considerable resources will continue to be channeled into developing Timberland’s global presence in the mining sector.